
Lean methodology applied in ABB’s production to optimise waste management
– Resulting in UL2799A Zero Waste to Landfill platinum validation!
Post Mil-teks modifications to their waste handling processes, the ABB Frosinone plant in Italy received the highest validation possible of the UL 2799A Environmental Claim Validation Procedure for Zero Waste Classifications
One of several outcomes of the changes was an 80% decrease in internal forklift usage!
0%
Zero Waste to Landfill Validation – platinum rating
ABB is a global technology company with a comprehensive portfolio of products, systems and services ranging from power grids and automation solutions to industrial robots and electrical components.
One of ABB’s factories is located in Frosinone, Italy, and this factory plays an important role in ABB’s overall “Mission to Zero” goal of being carbon neutral by 2030.
To reach this goal, changes needed to be made with regards to their waste handling. So they teamed up with Mil-tek!
The result of our cooperation has been a platinum rating validation according to the UL 2799A Environmental Claim Validation Procedure for Zero Waste Classifications. In order to achieve the highest “platinum” rating, a facility must prove that it consistently achieves a landfill waste diversion rate of 100%.
Let’s take a look at how it was made possible…

Lean processes, handling optimisation and compacting equipment
In order to observe the manufacturing processes and operator movements at the Frosinone plant, Mil-tek conducted thorough value stream mapping.
The analysis revealed, among other things, that trucks travelled an average of 11,000 km per year around the factory just to handle waste.
As a result of the investigation, ABB Frosinone optimised waste handling within their production by using a Lean compacting strategy that included installation of Mil-tek balers and leaner handling procedures in general.
With the introduction of a more efficient waste management, the trucks now travel an average of 2,200 km – a reduction of 80%!
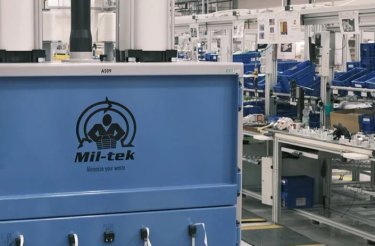
Easy installation of machines and many benefits
In the case of ABB, we installed a range of pneumatic balers in the production. These reduce waste volumes – like cardboard and plastics – by up to 90%, thus cutting the number of trips to outside containers.
Having no electrical or hydraulic components, the Mil-tek pneumatic balers could be installed directly on the production line to maximise efficiency and are powered by the factory’s existing compressed air lines.
Overall benefits for ABB are:
– waste handling is leaner
– use of forklift truck reduced by 80%
– the risk of accidents has been significantly reduced
– reduction in number of outdoor containers
– time freed up for more valuable tasks
– and much more…
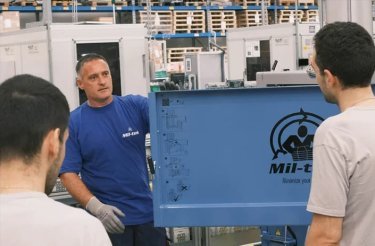
Do you have questions?
Contact us today to learn how Mil-tek can help your company save time, space and money by managing waste better.