Lean waste management
This page explores how applying Lean principles to waste handling reduces non-value-adding processes, saving time, space, and money through smarter, more efficient workflows.
What is Lean?
Lean is a management philosophy and operational approach focused on maximizing value while minimizing waste. Originally developed in the manufacturing sector, it has since been adopted across industries to streamline processes, improve efficiency, and enhance overall performance. At its core, Lean is about delivering more value to the customer with fewer resources. This is achieved not by working harder or faster, but by working smarter, eliminating anything that doesn’t directly add value.
Core principles of Lean explained below:

1. Continuous improvement (Kaizen)
Lean encourages a culture where everyone contributes to ongoing improvements. “Kaizen” means making small, incremental changes that collectively lead to significant gains in productivity, quality, and efficiency. It empowers teams to identify issues and propose practical solutions.
2. Elimination of waste
A key principle of Lean is identifying and removing waste from every process. The eight types of waste are remembered using the acronym TIMWOODS:
Transport – Inventory – Motion – Waiting – Overproduction – Over-processing – Defects – Skills (underused talent)
Reducing these wastes leads to smoother operations and better use of time and resources.
3. Value stream mapping
This tool helps visualize the flow of materials and information through a process. By mapping each step, organizations can identify where value is added, and where it’s lost, to guide improvement efforts.
4. 5S workplace organization
5S is a system for creating order and efficiency in the workplace:
- Sort – Remove unnecessary items
- Set in order – Organize tools and materials for easy access
- Shine – Clean the workspace regularly
- Standardize – Create consistent procedures
- Sustain – Maintain and review standards
A sixth “S” is often added: Safety, emphasizing that a clean, organized workplace must also be safe.
When waste handling isn’t Lean
In many facilities, waste like cardboard and plastic is collected in small bins placed throughout the site. These bins need to be emptied multiple times a day and transported, often by forklift, to outdoor containers. There, the material must be sorted, broken down, and reloaded.
This process creates unnecessary motion, waiting time, and transport – all of which Lean aims to eliminate. It interrupts workflow, increases the risk of sorting errors, and raises the chance of accidents.
This inefficient internal handling is only part of the problem. The issues continue when waste reaches the external containers.
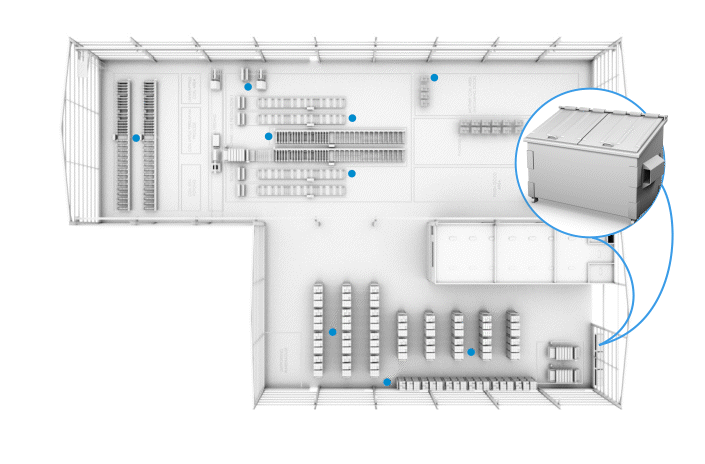
Standard external waste containers: Hidden inefficiencies
Relying on traditional outdoor waste containers brings several disadvantages:
-
Wasted time transporting materials and reloading them into containers
-
Low space efficiency, especially with uncompacted cardboard, plastic, and EPS
-
High collection costs, since containers are often emptied whether full or not
-
Sorting errors, leading to contamination and extra disposal charges
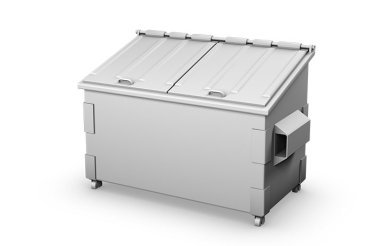
When waste handling involves constant transport, inefficient space use, and manual rework, it breaks with Lean principles, creating delays, extra costs, and wasted effort. Applying Lean to waste handling unlocks major gains in efficiency, safety, and cost control – both in manufacturing and beyond.
Advantages of Lean waste management
At Mil-tek, we apply Lean principles when designing waste solutions tailored to your workflow. Our balers and compactors are placed as close as possible to where the waste is generated, typically right at the unpacking area, as shown in the image on the right.
This setup allows waste to be handled immediately, without folding, sorting, or transporting it across the facility. Cardboard and plastic can go straight into a cardboard baler or plastic baler, where it’s compacted by up to 90%. When full, the machine indicates it’s time to empty, making the process simple and safe. The finished bales are compact, easy to store, and ready for efficient recycling pickup.
The result? A significantly more efficient workflow. You save time, free up valuable space, and reduce container and collection costs – all by aligning your waste management with Lean thinking.
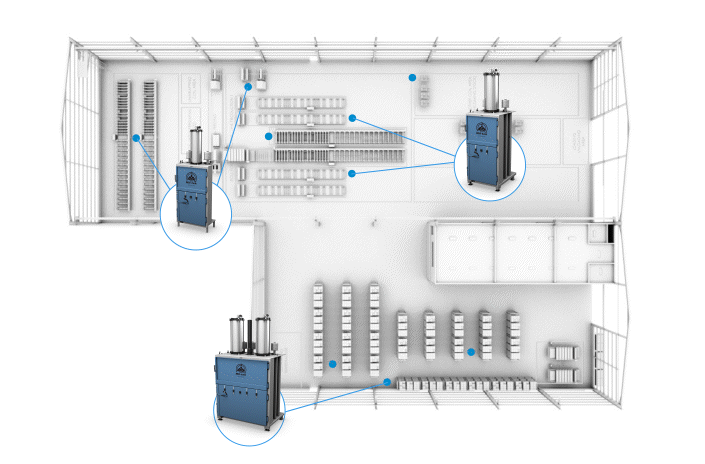
Lean waste management minimizes Forklift Truck use
In addition to saving time, space, and costs, Lean waste management also has a significant impact on workplace safety, especially when it comes to forklift use.
Forklift-related accidents are among the most common and serious workplace incidents. The risk increases when forklifts operate in shared spaces with pedestrians or in cluttered transport areas. By compacting waste directly at the source, Lean waste management drastically reduces the need for forklift transport. Fewer trips mean fewer risks—and a safer, more organized work environment.
Reduce forklift trips by up to 10:1
When materials are compacted before transport, each trip can carry up to 10 times more. This not only cuts down on forklift traffic but also boosts efficiency and lowers fuel, labor, and maintenance costs.
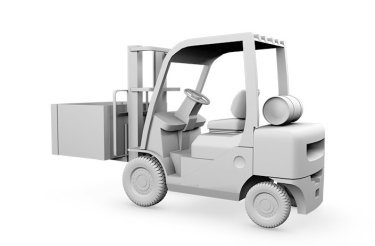
Curious how Lean principles can help you optimize waste handling?
Mil-tek can help you put Lean into action by implementing waste-minimizing solutions that reduce transport, save space, and improve efficiency, right where waste is generated.
Our systems are designed to support Lean workflows and help you turn waste handling into a streamlined, value-adding part of your operations.
Book a free site survey or contact us to learn more.
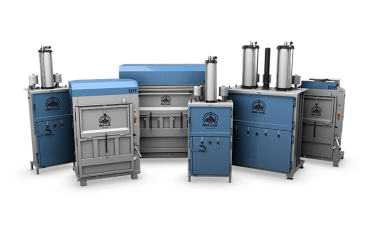
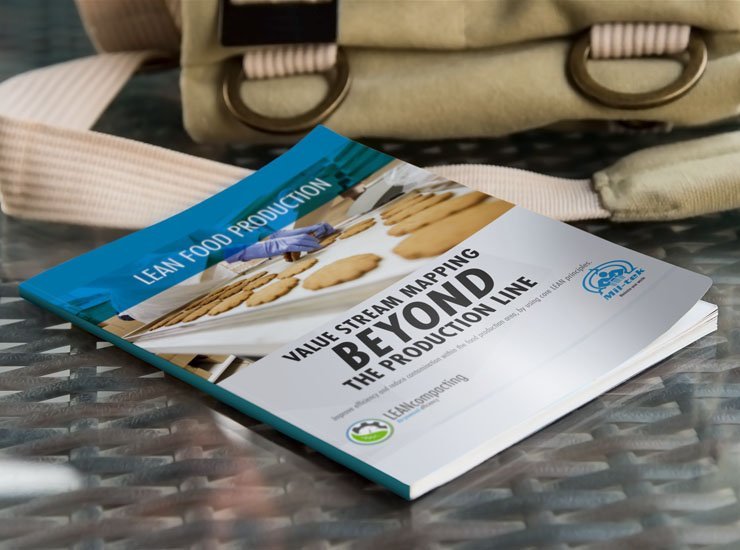
Contact us
Fill out the form below, and one of our experts will get back to you shortly with insights tailored to your needs.